Quality Assurance vs Quality Control: Key Differences Explained
Updated on : 14 April 2025
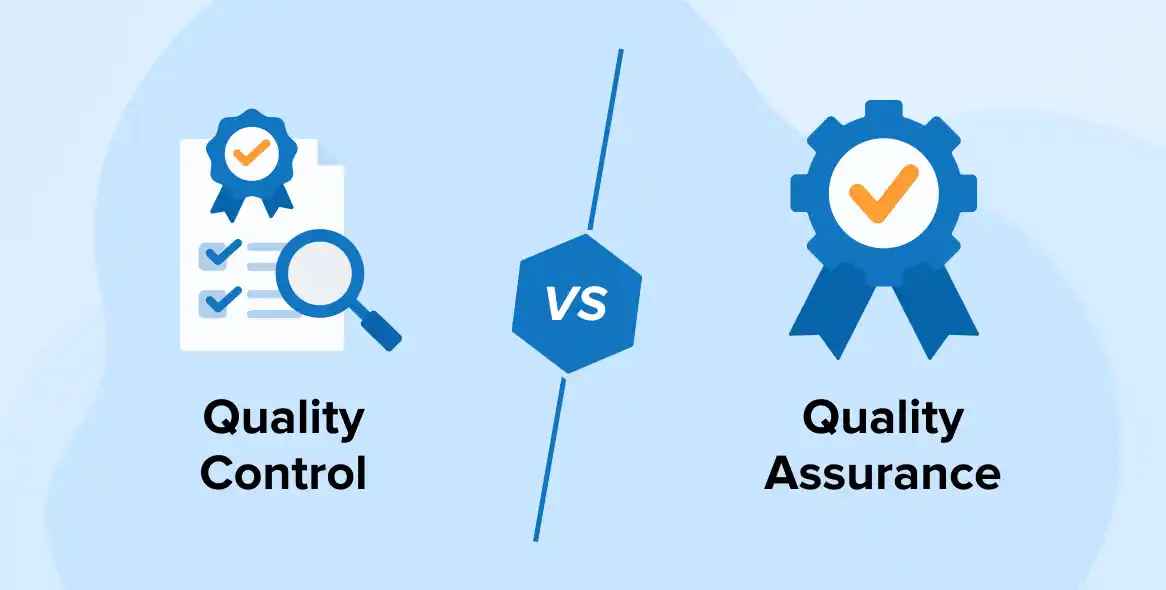
Image Source: google.com
Table Of Contents
- 1. Introduction
- 2. What is Quality Assurance (QA)?
- 3. What is Quality Control (QC)?
- 4. Key Differences Between Quality Assurance (QA) and Quality Control (QC)
- 5. Quality Assurance vs Quality Control
- 6. Advantages of Quality Assurance
- 7. Advantages of Quality Control
- 8. How QA and QC Work Together
- 9. Real-World Applications of QA and QC
- 10. Conclusion
- 11. FAQs
Table Of Contents
Introduction
Quality Assurance (QA)Quality Assurance and Quality Control (QC) are both critical in ensuring product quality, but they serve different purposes:
Quality Assurance (QA)
- Quality Assurance is a proactive process aimed at preventing defects by improving and ensuring the processes involved in production.
- It focuses on systematic activities that provide confidence the product will meet quality standards.
Quality Control (QC)
- Quality Control on the other hand, is a reactive process that involves identifying defects in the finished product through testing and inspection.
- It ensures that the product conforms to specific requirements and standards.
What is Quality Assurance (QA)?

Image Source: QA World
- Quality Assurance (QA) is a systematic and proactive process focused on ensuring that the methods, procedures, and standards used during production lead to high-quality outcomes.
- Its primary goal is to prevent defects and ensure that the final product meets the required quality standards.
Purpose of QA:
-
To improve development and testing processes.
-
To prevent defects before they occur.
-
To ensure consistency and compliance with industry standards and customer requirements.
-
To build confidence in the quality of the product or service.
Quality Assurance Overview
Aspect | Description |
---|---|
Definition | A proactive, process-oriented approach to prevent defects and ensure quality. |
Primary Purpose | To improve processes and prevent issues before they occur. |
Focus Area | Process-oriented: focuses on how the product is made or developed. |
Goal | To ensure consistent quality by refining and following standardized processes. |
Common Quality Assurance Techniques
Technique | Description |
---|---|
Process Checklists | Verify that standard procedures are being followed. |
Audits | Regular evaluations of processes for compliance and effectiveness. |
Process Standardization | Use of SOPs (Standard Operating Procedures) for consistency. |
Training & Development | Equip teams with skills and knowledge to maintain quality. |
Documentation Review | Ensure accuracy and completeness of documentation. |
Continuous Improvement | Use of models like PDCA (Plan-Do-Check-Act) for ongoing process enhancement. |
For Quality Assurance Services
Ensuring flawless performance and reliability through rigorous quality assurance at Hexadecimal Software.
What is Quality Control (QC)?
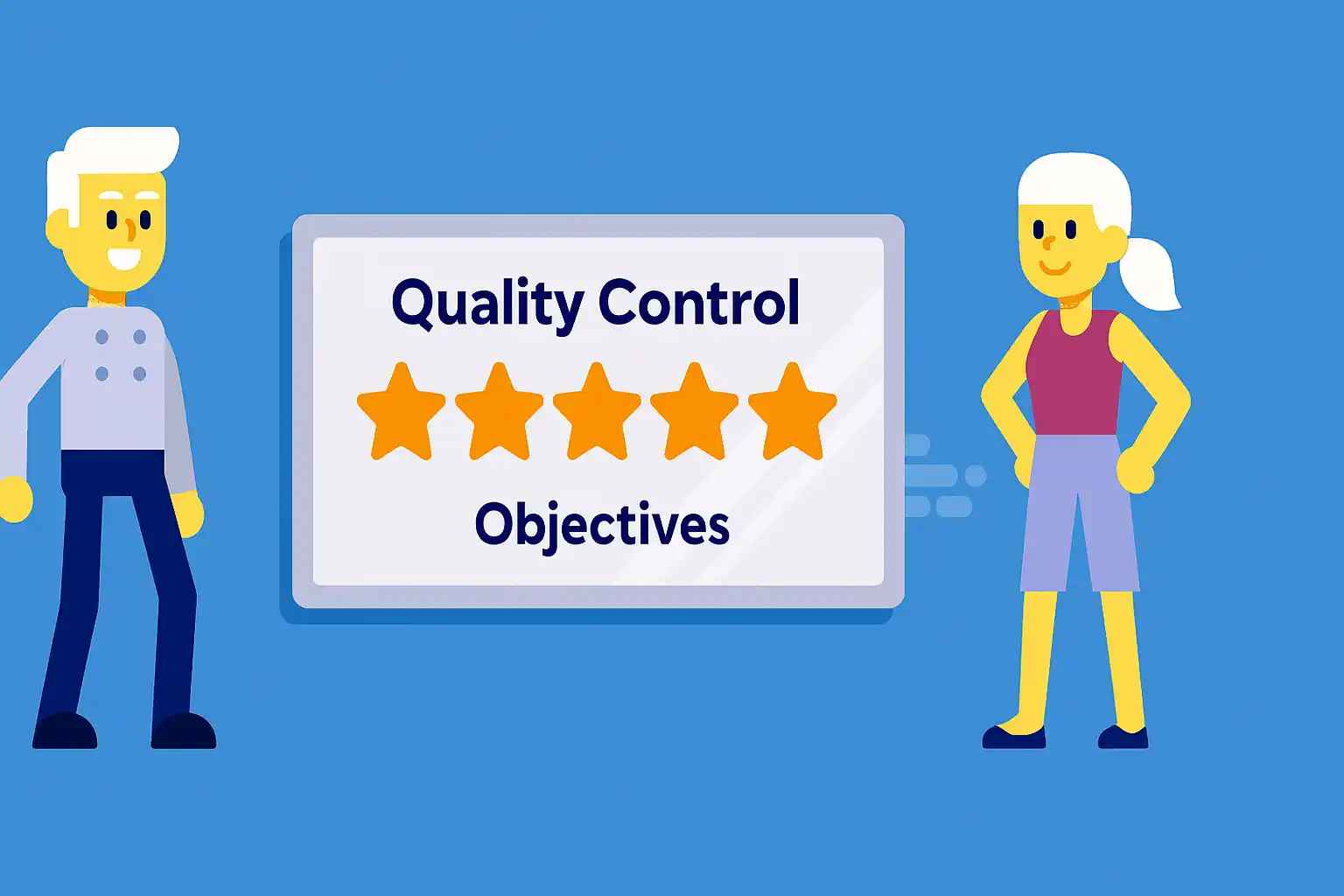
Image Source: google
- Quality Control (QC) is a product-oriented, reactive process that focuses on identifying and fixing defects in the final product.
- It involves inspection, testing, and review to ensure the product meets specified standards and customer expectations.
Objectives of QC:
-
To detect defects in the final product.
-
To ensure the product meets predefined quality standards.
-
To verify that processes produce consistent and acceptable outputs.
-
To maintain customer satisfaction by delivering defect-free products.
Quality Control Overview
Aspect | Description |
---|---|
Definition | A product-oriented, reactive process focused on identifying and fixing defects in the final product. |
Primary Objectives | To detect defects and ensure the product meets predefined quality standards. |
Focus Area | Product-oriented: emphasizes the output or final product. |
Goal | To deliver defect-free products that meet customer expectations. |
Delivering bug-free user experiences through meticulous manual testing at Hexadecimal Software.
Common Quality Control Methods
Method | Description |
---|---|
Inspection | Manual or automated checks to detect defects in the product. |
Testing | Includes functional, performance, and stress testing to validate product behavior. |
Statistical Quality Control (SQC) | Uses statistical tools like control charts and sampling techniques. |
Peer Reviews | Team members examine the product or code for errors and improvements. |
Validation & Verification | Confirms the product meets requirements and performs as intended. |
Key Differences Between Quality Assurance (QA) and Quality Control (QC)
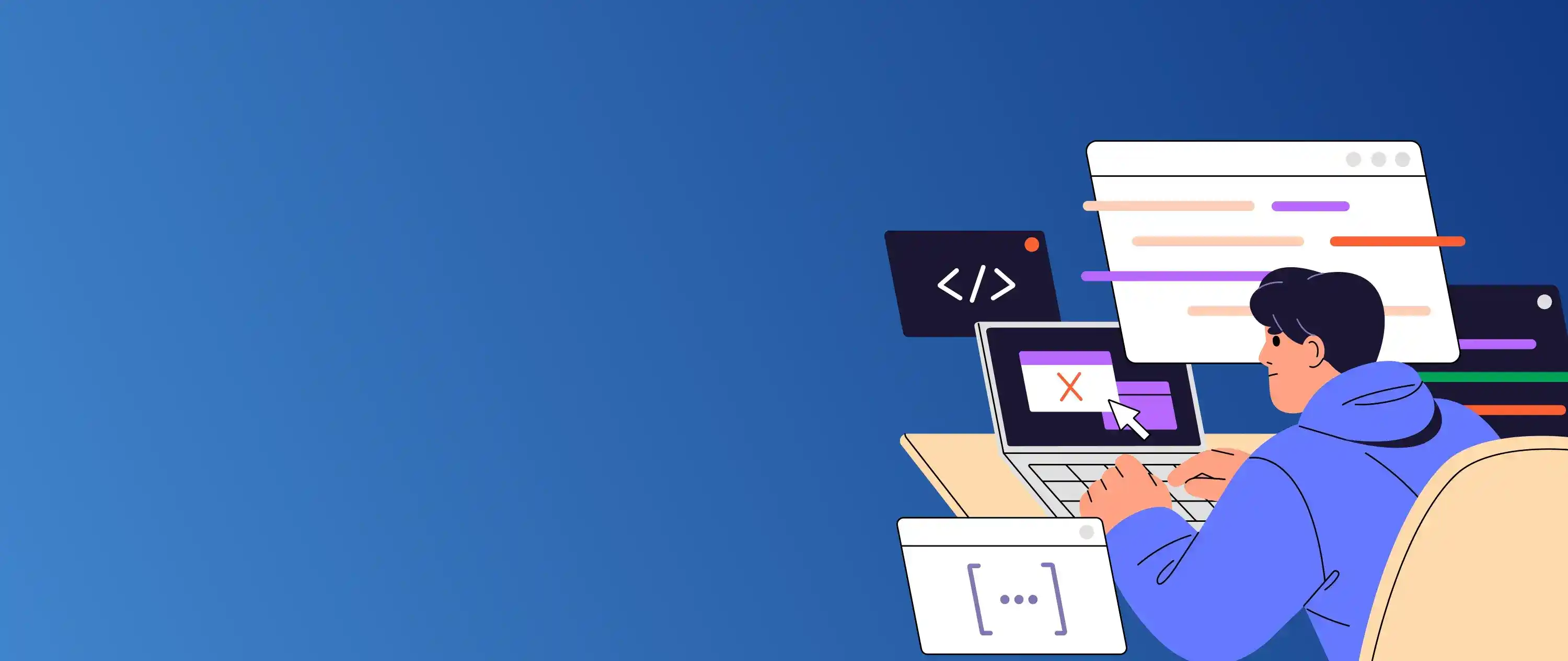
Want to ensure top-notch quality in your enterprise solutions?
Aspect | Quality Assurance | Quality Control |
---|---|---|
Definition | A proactive, process-oriented approach to prevent defects. | A reactive, product-oriented approach to identify and fix defects. |
Focus | Improves and ensures the process. | Examines the final product for issues. |
Objective | To prevent defects by refining processes. | To detect and correct defects in the product. |
Timing | Performed throughout the development process. | Performed after the product is developed. |
Responsibility | Everyone involved in the process (developers, analysts, etc.). | Dedicated testing or inspection team. |
Approach | Preventive (process-focused). | Corrective (product-focused). |
Techniques Used | Process checklists, audits, training, documentation review. | Testing, inspection, statistical quality control, validation. |
Definition:
-
QA is a proactive and process-oriented approach that ensures quality by improving and controlling the development process.
-
QC is a reactive and product-oriented approach that focuses on identifying and fixing defects in the finished product.
Focus:
-
QA focuses on how the product is made — it’s all about the process.
-
QC focuses on what is made — the final product is examined for quality.
Objective:
-
QA aims to prevent defects before they occur by refining processes and standards.
-
QC aims to detect, isolate, and fix defects after the product is developed.
Timing:
-
QA activities are carried out throughout the software or product development life cycle.
-
QC activities are performed after development, during or after production.
Responsibility:
-
QA is a responsibility shared by everyone involved in the development process (developers, analysts, managers, etc.).
-
QC is usually performed by a specific team, such as testers or inspectors.
Approach:
-
QA follows a preventive approach, aiming to improve processes to avoid issues.
-
QC follows a corrective approach, aiming to identify and fix issues after they occur.
Techniques Used:
-
QA involves techniques like audits, process checklists, training, and documentation reviews.
-
QC involves techniques like functional testing, inspections, statistical quality control, and validation.
For API automation Testing Services
Ensuring robust backend performance through efficient API automation testing at Hexadecimal Software.
Quality Assurance vs Quality Control
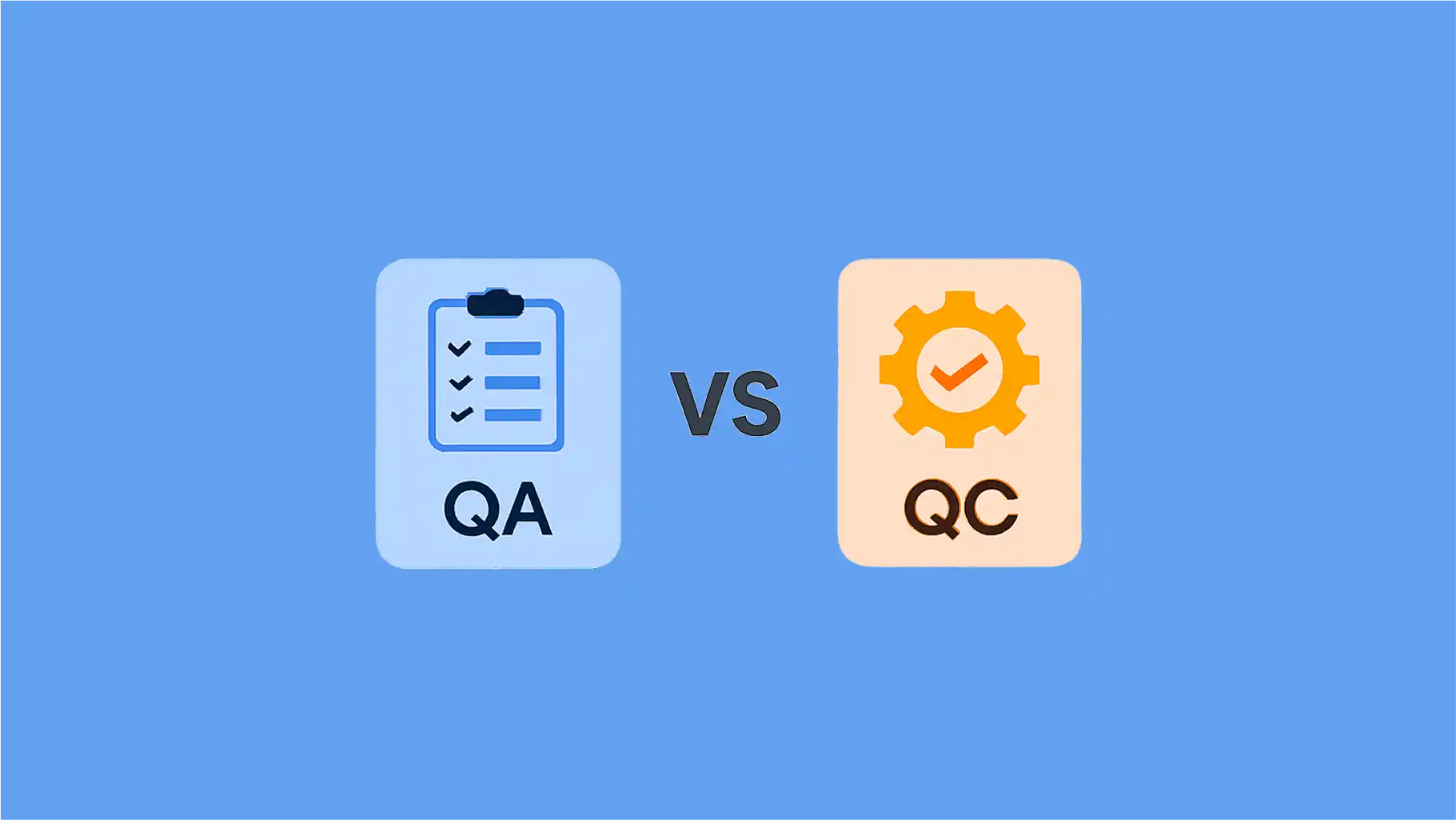
Image Source: google
Parameter | Quality Assurance | Quality Control |
---|---|---|
Purpose | Prevent defects by improving processes. | Identify and fix defects in the final product. |
Techniques | Audits, checklists, training, process reviews. | Inspection, testing, defect tracking. |
Scope | Focuses on the development process. | Focuses on the final product. |
Timing | Continuous throughout development. | Performed after development or production. |
Responsibility | Everyone in the project. | Typically the testing or QC team. |
Approach | Proactive: process-focused. | Reactive: product-focused. |
Outcome | Improved processes, fewer defects over time. | Defect-free final product. |
Tools | Process management, risk analysis. | Automated/manual testing tools, defect tracking. |
Feedback Loop | Ongoing process improvement. | Fixing defects before delivery. |
Advantages of Quality Assurance
Advantage | Description |
---|---|
Prevention of Defects | Catches issues early, preventing defects. |
Improved Quality | Ensures products meet standards. |
Cost Reduction | Minimizes rework and saves costs. |
Consistency | Standardizes processes for uniform quality. |
Customer Satisfaction | Meets customer expectations for better satisfaction. |
Faster Time to Market | Reduces rework, speeding up release. |
Compliance | Ensures regulatory compliance and reduces risks. |
Continuous Improvement | Promotes ongoing process refinement. |
Prevention of Defects:
- QA focuses on identifying potential issues early in the development process, preventing defects before they happen.
- This approach reduces the likelihood of problems occurring in the final product.
Improved Product Quality:
- QA ensures that the product meets the required standards and performs as expected.
- It guarantees the final product is consistent and high quality, leading to fewer issues post-release.
Cost Reduction:
- By addressing defects and inefficiencies early in the development process, QA reduces the need for expensive rework and fixes later on.
- This leads to a more cost-effective product development process.
Consistency:
- QA establishes standardized processes, ensuring consistency in every product release.
- This uniformity ensures that each product meets quality expectations, regardless of who develops it.
Customer Satisfaction:
- A primary goal of QA is to meet or exceed customer expectations.
- By focusing on quality, QA ensures that the product is reliable, functional, and user-friendly, leading to higher customer satisfaction and loyalty.
Faster Time to Market:
- With effective QA processes in place, issues are caught earlier, reducing delays.
- This allows the product to reach the market faster, without needing extensive revisions or fixes during the later stages of development.
Compliance and Risk Management:
- QA ensures that products adhere to industry standards, certifications, and regulatory requirements.
- This reduces the risk of legal issues, penalties, or product recalls due to non-compliance.
Continuous Improvement:
- QA encourages a culture of continuous improvement.
- By regularly evaluating and refining processes, it helps teams enhance their workflows and achieve better results with each new development cycle.
For Mobile App Testing Services
Validated seamless user experiences across diverse devices through meticulous mobile app testing at Hexadecimal Software.
Advantages of Quality Control
Advantage | Description |
---|---|
Detection of Defects | Identifies issues in the final product before release. |
Assured Quality | Verifies product meets defined quality standards. |
Cost Management | Avoids costly post-release fixes by catching errors early. |
Process Reliability | Maintains consistency through rigorous testing. |
Customer Confidence | Delivers reliable products that build customer trust. |
Efficient Delivery | Prevents delays by ensuring product readiness. |
Regulatory Assurance | Verifies compliance with industry standards and regulations. |
Product Enhancement | Provides feedback for improving product quality. |
Defect Detection:
- QC helps in identifying defects in the product before it reaches the customer.
- Through systematic inspection and testing, QC ensures that the final product is free from defects.
Improved Product Quality:
- QC ensures that the final product meets the desired quality standards and specifications.
- It helps maintain consistency and reliability in the product’s performance.
Ensuring Customer Satisfaction:
- By detecting and correcting defects, QC ensures that the product aligns with customer expectations.
- This leads to increased customer satisfaction and trust in the product.
Risk Mitigation:
- QC identifies and corrects issues early, minimizing the risk of defective products being shipped to customers.
- This reduces the likelihood of product recalls or legal liabilities.
Cost Efficiency:
- By addressing defects early in the process, QC prevents the production of large batches of defective products, saving costs associated with returns, repairs, or replacements.
Compliance with Standards:
- QC ensures that products comply with industry-specific standards, regulations, and certifications.
- This ensures that the product can be legally marketed and meets all quality requirements.
Enhanced Brand Reputation:
- Products that pass through thorough QC testing are less likely to have defects, which helps build a positive brand reputation for quality and reliability.
Continuous Improvement:
- QC provides feedback for improvement by identifying recurring issues or patterns in defects, helping improve manufacturing processes and product design in the long run.
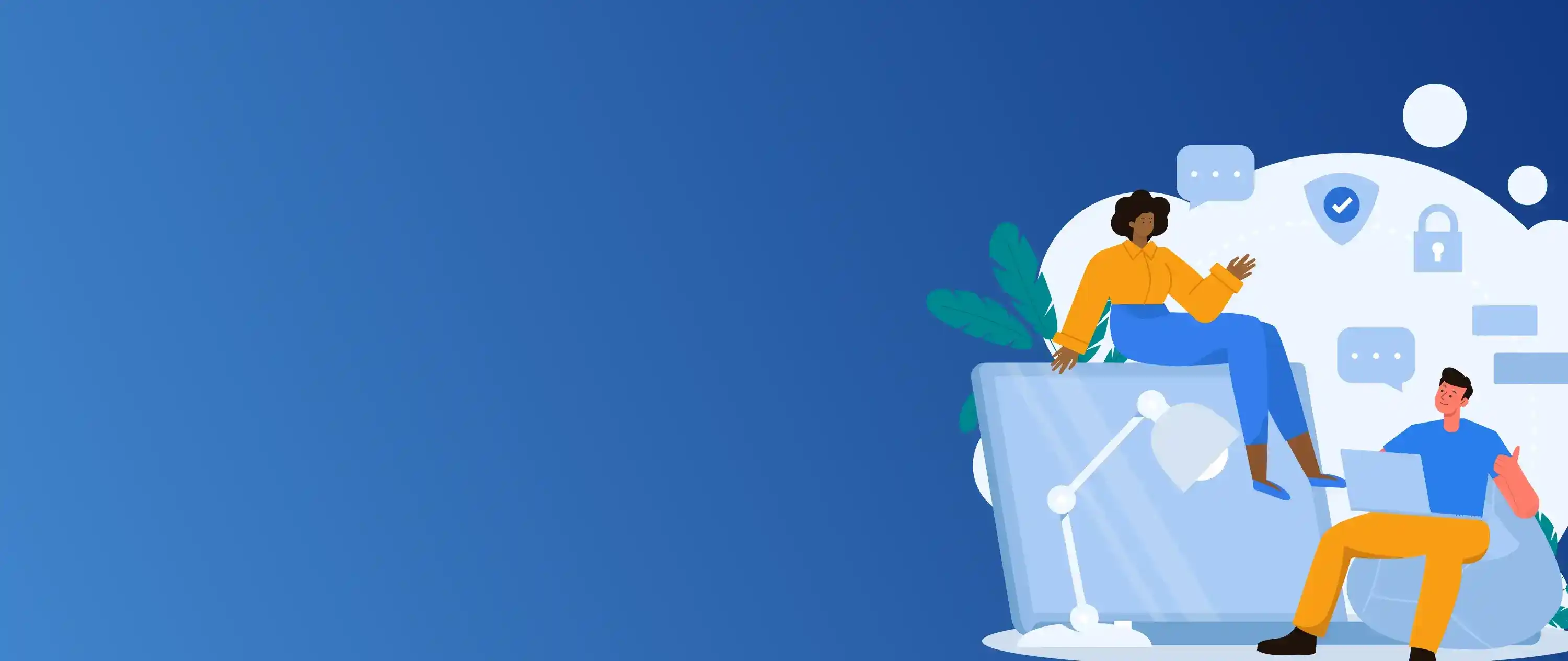
Explore Quality Assurance services by Hexadecimal Software.
How QA and QC Work Together
Aspect | Quality Assurance | Quality Control |
---|---|---|
Approach | QA is proactive: it aims to prevent defects before they happen. | QC is reactive: it focuses on identifying and correcting defects after the product is made. |
Primary Focus | QA focuses on process improvement to make sure defects don't occur. | QC focuses on the end product to verify it meets quality standards. |
Timing | QA works throughout the development process, from planning to release. | QC works towards the end of the development, ensuring the final product is defect-free. |
Goal | QA ensures that the processes used in production are robust and efficient. | QC ensures that the final product is up to standard and matches customer requirements. |
Feedback Loop | QA improves processes based on past data and audits. | QC provides immediate feedback by finding defects and pushing for corrections. |
Risk Management | QA reduces risks by fixing processes and preventing defects. | QC reduces risks by catching defects in the final product, preventing faulty deliveries. |
Customer Satisfaction | QA ensures that products are developed to meet customer needs from the start. | QC ensures that the delivered product matches customer expectations and is defect-free. |
Collaboration | QA works with development teams to create quality processes and frameworks. | QC collaborates with production teams to inspect and test the final product. |
Efficiency | QA helps reduce costs by streamlining development processes. | QC ensures that no defective products are released, preventing expensive recalls or returns. |
Continuous Improvement | QA fosters ongoing improvement of processes, resulting in long-term quality gains. | QC identifies product-related issues that lead to process improvements for future projects. |
Ensured robust and reliable web applications through efficient automation testing practices at Hexadecimal Software.
Real-World Applications of QA and QC
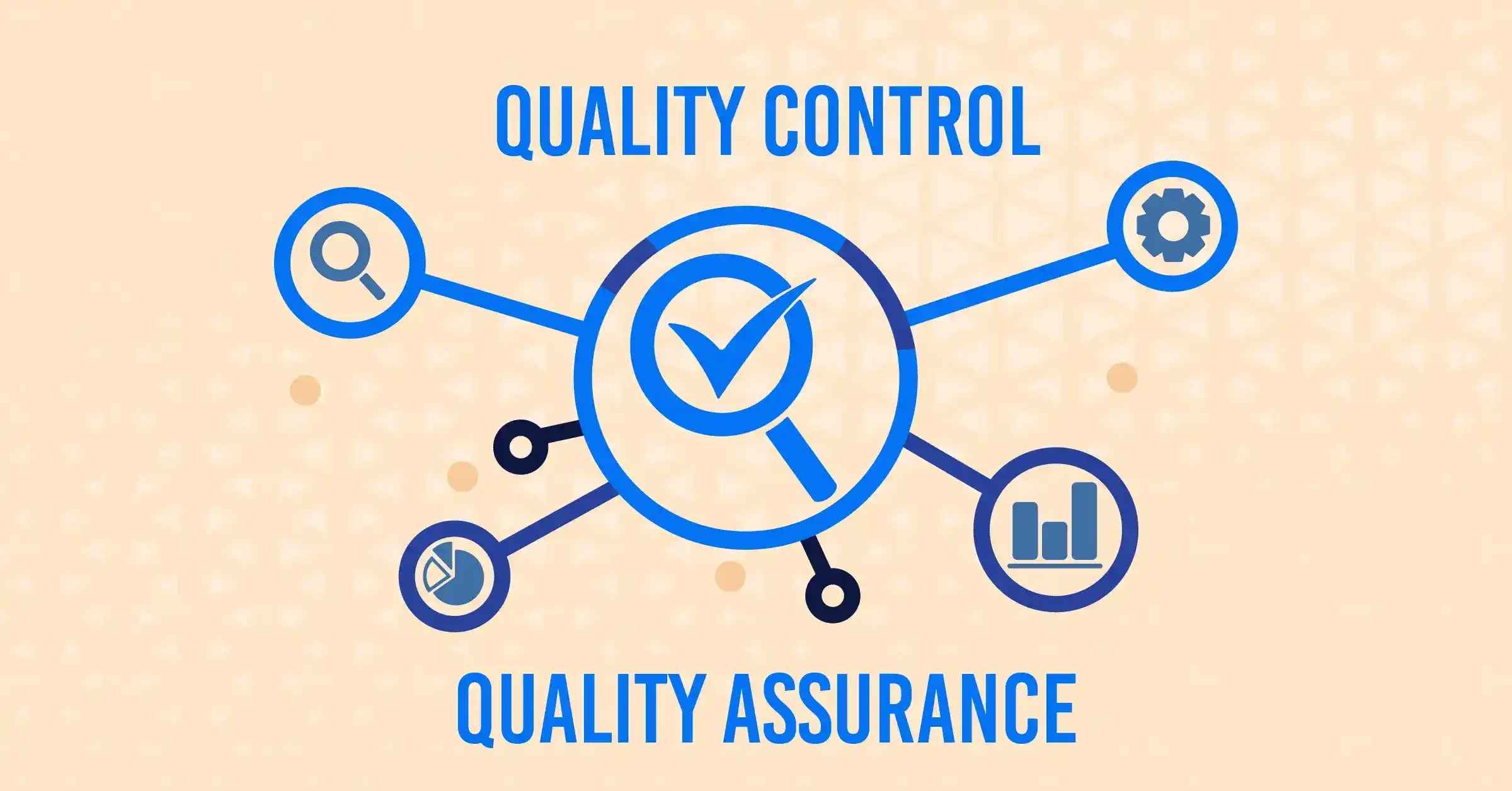
Image Source: google
- QA focuses on improving the process and preventing defects from happening, while QC focuses on inspecting the final product to ensure it meets quality standards.
- Both QA and QC are essential for delivering a high-quality product in any industry, ensuring safety, customer satisfaction, and compliance with regulations.
Software:
-
QA: Establishes best practices and processes to prevent bugs and improve development efficiency.
-
QC: Focuses on testing the software to find and fix bugs, performance issues, and functionality errors before release.
Manufacturing:
-
QA: Optimizes and standardizes production processes to minimize errors and improve efficiency.
-
QC: Inspects finished products to ensure they meet specifications, detecting any defects or inconsistencies.
Pharmaceuticals:
-
QA: Develops processes and guidelines to ensure drugs are manufactured safely and consistently according to regulations.
-
QC: Tests the final products (drugs) for quality, potency, and compliance with health regulations before they reach consumers.
Automotive:
-
QA: Creates production standards and processes to reduce defects in vehicles and ensure safety.
-
QC: Inspects vehicles after production to detect and correct any defects or issues before the product is sold.
Food:
-
QA: Establishes food safety standards and procedures to ensure safe and consistent food production.
-
QC: Monitors and tests food products for quality, consistency, and safety during production and before packaging.
Aerospace:
-
QA: Ensures that manufacturing processes comply with rigorous safety and quality standards for aerospace products.
-
QC: Inspects parts, assemblies, and systems to detect defects and ensure they meet strict safety requirements.
Electronics:
-
QA: Develops quality standards and ensures manufacturing processes are followed to maintain high product quality.
-
QC: Inspects final products like smartphones or computers to check for defects in functionality, performance, and appearance.
Construction:
-
QA: Ensures that construction processes, materials, and methods meet safety and quality standards.
-
QC: Inspects the completed structure to ensure it is safe, durable, and complies with regulatory standards before being used.
Conclusion
Quality Assurance (QA) and Quality Control (QC) are both vital for achieving high product quality.
-
QA focuses on preventing defects by improving processes and ensuring quality standards throughout development.
-
QC checks the final product to find and fix any defects, ensuring it meets specifications and customer expectations.
Together, QA and QC ensure products are reliable, safe, and meet the required standards, leading to higher customer satisfaction and trust.
FAQs
Q.1. What is the difference between Quality Assurance (QA) and Quality Control (QC)?
A : QA focuses on improving processes to prevent defects, while QC involves inspecting the final product to detect and fix defects before it reaches customers.
Q.2. Why is Quality Assurance important in product development?
A : QA helps prevent defects early in the development process by establishing standards and improving processes, leading to a more reliable and consistent product.
Q.3. How does Quality Control ensure product quality?
A : QC involves inspecting and testing the final product to ensure it meets specifications and customer expectations, identifying any defects or issues before the product is released.
Q.4. Can a product have QA without QC?
A : Yes, a product can have QA without QC, but having both ensures a higher level of quality. QA prevents defects early, and QC ensures the final product meets the required standards.
Q.5. What industries apply both QA and QC?
A : Industries like software, manufacturing, pharmaceuticals, automotive, food, electronics, aerospace, and construction use both QA and QC to ensure product safety, performance, and customer satisfaction.